News
A kiln must never be a bottleneck
Martinsons in Bygdsiljum was the first company in Sweden to produce cross-laminated timber (CLT). They have produced the material since 2007, and in 2017 they tripled their capacity by investing in a new production line.
"The market is really positive about the product. Up until now, we've been working hard to convince people and the last 15 years were pretty tough going. But these days, people in the industry come to us expressing their interest," says production manager Olov Martinson.
A number of Swedish sawmills are investing in the product, and in 2019 Martinsons was joined in the Swedish market when Stora Enso's new CLT production line was completed in Grums. Furthermore, Södra Timber has opened a factory next to its sawmill in Värö, and Norway is also climbing aboard the CLT bandwagon with Splitkon in Åmot, about 60 miles west of Oslo, investing Euro 23.6 million in a new factory.
Martinsons truly got the wind in their sails when they supplied CLT to the eight story buildings in Strandparken in Sundbyberg.
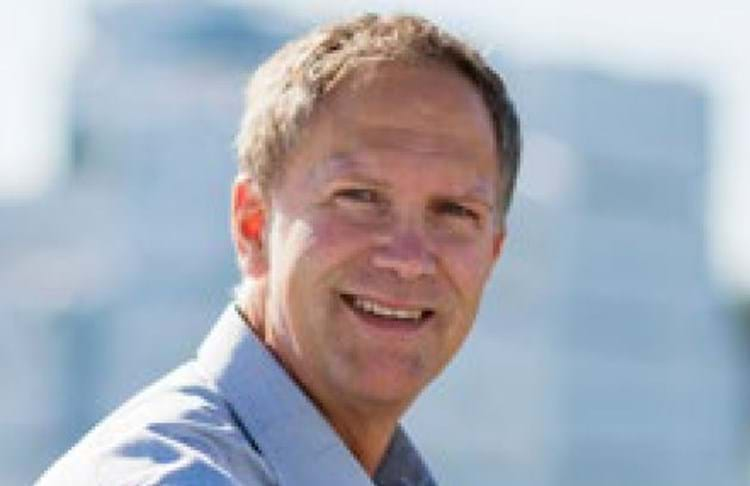
"We've carried out a lot of construction in Växjö and Skellefteå, but we attracted the most attention when we began construction in Sundbyberg. They have extensive experience with the material in Europe, but with the difference that Germany and Austria use it in lower buildings, such as single-family homes. In the Nordics,
the trend is for taller buildings, and it's here we are at our most competitive," says production manager Olov Martinson.
Martinsons feels that most of those who've chosen CLT will continue to do so in the future.
"This is a great testimony. I think you have to try it to be convinced,” says Olov.
Have changes in the drying process kept pace with your product development?
"Absolutely. Drying is what has the biggest impact, for better and for worse. When we do it right, it has a great effect on quality and capacity and we enjoy good flows and a stable process. If we compare with things a few years ago, there are now many good technical solutions, robust kiln buildings, smart analysis tools and monitoring processes that are of great help to operators," says Olov.
Never a bottleneck
In the Martinsons approach, kilns may never be a bottleneck. At the same time, lumber must get the time it needs in the kiln.
"Because we never scrimp on quality, volumes have to take second place. But building kiln capacity so we never end up in precarious situations has been a long journey. When the technology for managing drying is developed, times can also be cut. In the past, perhaps things went a bit too quickly and sometimes wrong. Today, things are more stable and we feel at ease with the process," he says.
Martinsons works through project groups whose watchwords are not just about high quality, but also the right quality.
"CLT is not an overly demanding product when it comes to kiln production. It has more to do with flows. The better the flow, the better the product. The kiln operators have to know what they’re drying.”
"We have different requirements depending on whether we’re sawing construction material, glulam or a product. It's not about better or worse, but about adapting the drying," says Olov, adding that it's also a matter of training the customer.
"It has to be properly dried," say customers, but in what way? Straight, or without tension? Perhaps the customer values qualities other than just a certain target moisture content."
Increased knowledge
The process has become more stable at Martinsons, and their knowledge has increased. According to Olov Martinson, this is where Valutec has played a major part for operators and mechanics.
"Collaboration with colleagues is extremely important, and Valutec is good at creating networks, which is a great help. If you've maybe met someone at a trade show, it’s easier to call and ask them about their experiences.