News
Swedish success story: Valutec hits half-century mark, over 50 TC continuous kilns sold in five years
In 2016, Valutec put Central Europe's first TC continuous kiln into operation at the Egger sawmill in Brilon/DE. That was the starting shot for a success story that has now continued with over 50 of these Swedish cross-flow dryers. We have to ask in Brilon how the TC performs in continuous use.
Last week 5071 stood on a package of sawn lumber at the outlet of the TC-kiln at Egger in Brilon. The number indicates the consecutive batch number since the system was started up five years ago. If you calculate around 100 cubic meters (42.4 MBF) for a batch, the dryer has so far achieved a system output of well over 500,000 cubic meters (211,888 MBF) of sawn lumber and thus well above the 80,000 cubic meters/yr (33,902 MBF) guaranteed by Valutec.
But from the beginning: In 2016, Valutec and Egger broke new ground in Central Europe with the TC kiln. The two companies realized together the first TC kiln outside Scandinavia at the sawmill and panel location in Brilon, creating a reference that attracted numerous wood industries from all over the world and led to over 50 further orders at Valutec.
Valutec Marketing Manager Eric Johansson names TC kiln deliveries to the Ziegler Group (DE), Mercer (DE), Hampton Lumber (US), Luzales (RU) Hasslacher Group (AUT) as examples.
In the TC kiln, the stacks are guided lengthways through zones in which the air flow moves at an angle of 90° to the feed direction. This enables separate climate control in the different kiln zones, which allows the operator to dry different dimensions at the same time, or to put it casually: results in several batch kilns connected in series. Valutec has thus succeeded in combining the flexibility of batch kilns with the low energy consumption and high throughput of a continuous kiln.
The TC kiln at Egger in Brilon has been running for five years without any significant disruptions and not a single unplanned downtime.
Courage was rewarded
“It was a big step back then, but today we are proud and happy to operate the first TC kiln in Central Europe. Looking back, it was the right decision and a good time on top of that”, reports Paul Lingemann, the sawmill's technical director.
As one of the great challenges, Lingemann remembers the different input moisture levels compared to fresh goods in Scandinavia, which result from the larger round lumber dimensions and the multi-stemmed incision. In the end, this large dispersion of the input moisture for the TC kiln, due to the ingenious drying programs, has never been a problem. Originally intended for side goods, Egger now uses the channel for main goods up to 40 mm thick if required.
Another major hurdle that Lingemann remembers was the extremely low inlet temperature of only 80 °C (104 F). “The heat generated by the biomass power plant goes first to the chipboard and MDF production and only then comes to us. We use it to dry the sawn timber even more gently and also lower the return temperature of the power plant, which increases its efficiency,” explains the managing director of the process and adds that this hurdle was overcome in close cooperation.
Lingemann particularly appreciates the Swedes' approach here: “A culprit was never looked for, but always looked ahead and found a solution together.” An assessment that, according to Johansson, also applies exactly to the Egger team in Brilon.
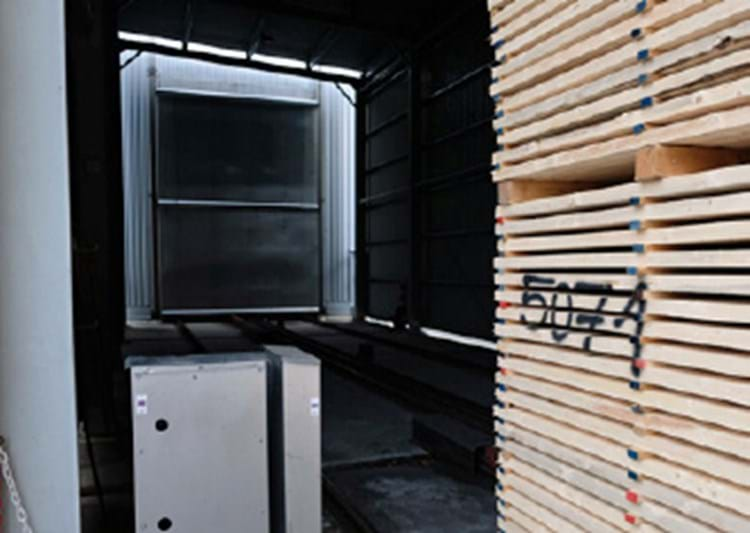
5071 batches of 100 cubic meters (42.4 MBF) each makes more than
500,000 cubic meters (211,888 MBF) throughput in the past five years – significantly more than Valutec promised.
40,000 cubic meters (16,951 MBF)/yr for free
With the investment in the TC canal, the output in Brilon has also grown considerably in recent years. Egger increased production from 15 to 20 shifts per week and also made numerous investments in optimization and automation, which increased lumber production from 360,000 cubic meters (152,559 MBF)/yr to 580,000 cubic meters (245,790 MBF)/yr.
Lingemann puts the annual output of the TC sewer at over 120,000 cubic meters (50,853 MBF)/ today. That is 40,000 cubic meters (16,951 MBF)/yr more than originally promised by Valutec.
“With the 80,000 cubic meters (33,902 MBF)/yr, we did not miscalculate, but only promised what we can safely fulfill with regard to the best possible drying quality,” Johansson explains the company philosophy and Lingemann adds that the drying quality is still good even at 120,000 cubic meters (50,853 MBF)/yr.
Eric Johansson from Valutec together with Paul Lingemann, Christoph Kurtz and Bernd Wagner from Egger in front of the TC tunnel dryer in Brilon.
100% availability
After five years of continuous operation, Lingemann estimates the technical availability of the system at 99% and Christoph Kurtz, responsible for wood drying, believes that this should be rated even higher: “Since commissioning, we have not had a single unplanned downtime and hardly any maintenance work. If overhaul work is to be carried out, this can be carried out from the above located technical room without any problems."
At the moment, Brilon is well positioned with a combination of a TC kiln and fresh air/exhaust air chambers. "However, if the chambers are getting old in a few years, and a replacement investment is due, Valutec will certainly be our first point of contact again," Lingemann concludes.
Text & photo: Gunter Jauk, Holzkurier
Downloads
Contacts
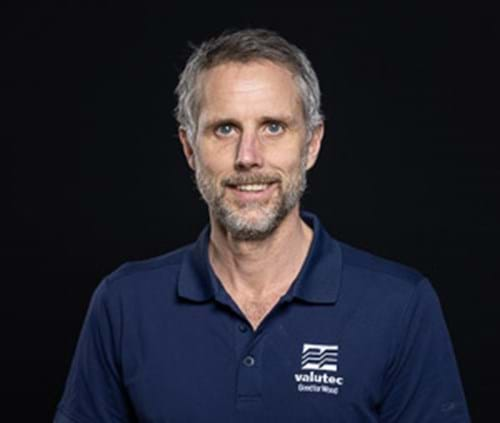
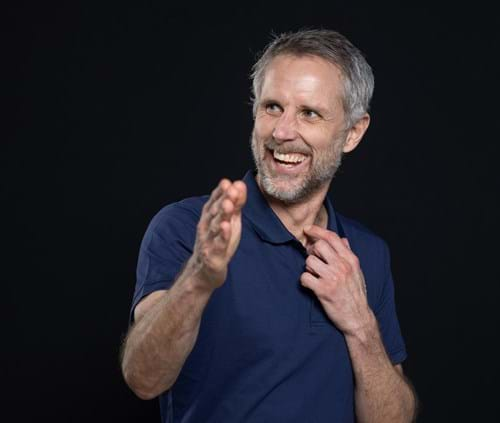